Innovations In High-Quality Tailings dewatering screen Meshes: Enhancing Efficiency And Sustainability
In the realm of mining and mineral processing, the management of tailings has long posed significant environmental and operational challenges. Tailings, the byproduct of extracting valuable minerals from ore, are typically slurry of water and waste. As industries strive for more sustainable practices, the focus on efficient tailing management has intensified, leading to innovations in dewatering technologies. Among these, high-quality tailings dewatering screen meshes stand out as a pivotal advancement, enhancing both efficiency and sustainability in mineral processing operations. Dewatering screen meshes are engineered to separate water from solids, a critical process in reducing the volume of tailings. This reduction is crucial as it directly correlates with a decrease in the footprint of tailings dams and the associated risks of dam failures, which have had catastrophic environmental and human safety impacts in the past. The latest innovations in screen mesh design are tailored to maximize water removal while ensuring the retention of fine particles, which are often challenging to manage. The material used in these advanced screen meshes is a key element of their effectiveness. High-tensile, stainless steel wire is commonly employed for its strength and resistance to abrasion, which are essential for handling the abrasive nature of tailings. This durability not only extends the lifespan of the screens but also reduces the need for frequent replacements, thereby enhancing operational efficiency and reducing downtime.Moreover, the configuration of the mesh plays a critical role in optimizing performance. Modern dewatering screens are designed with a specific aperture size and shape that facilitate the rapid movement of water through the mesh while capturing finer materials. This specificity not only improves the dewatering process but also aids in the recovery of materials that can be recycled or sold, adding a valuable stream of revenue. The precision in design also minimizes blockages and maintenance requirements, further boosting productivity. The environmental benefits of using high-quality tailings dewatering screen meshes are significant. By efficiently separating water from the waste, these meshes enable the reuse of water in the milling process, reducing the demand for fresh water and minimizing the volume of water that needs to be managed or treated. This is particularly important in arid regions where water scarcity is a pressing issue. Additionally, drier tailings are more stable and can be more easily managed or repurposed, thereby reducing the environmental footprint of mining operations. The integration of these advanced screen meshes into tailings management systems also aligns with broader industry trends towards automation and real-time data monitoring. Many modern dewatering screens are equipped with sensors that provide continuous feedback on performance and moisture content, allowing for adjustments to be made in real time. This capability not only enhances the efficiency of the dewatering process but also contributes to the overall optimization of mineral processing operations. In conclusion, the development of high-quality tailings dewatering screen meshes represents a significant step forward in the mining industry’s quest for more efficient and sustainable practices. By combining robust materials with innovative designs, these meshes improve operational efficiencies, reduce environmental impacts, and contribute to the safer management of tailings. As the industry continues to evolve, these technologies are set to play a crucial role in shaping the future of mineral processing.
Comparing Different Materials For High-Quality Tailings Dewatering Screen Meshes: Performance And Cost Analysis
Tailings dewatering screen meshes are critical components in the mining and mineral processing industry, where they are used to separate solids from liquids, enabling the recovery of valuable minerals and the responsible management of waste materials. The effectiveness and efficiency of a tailings dewatering screen largely depend on the quality of the screen mesh material used. This article provides a comparative analysis of different materials used in high-quality tailings dewatering screen meshes, focusing on their performance and cost implications.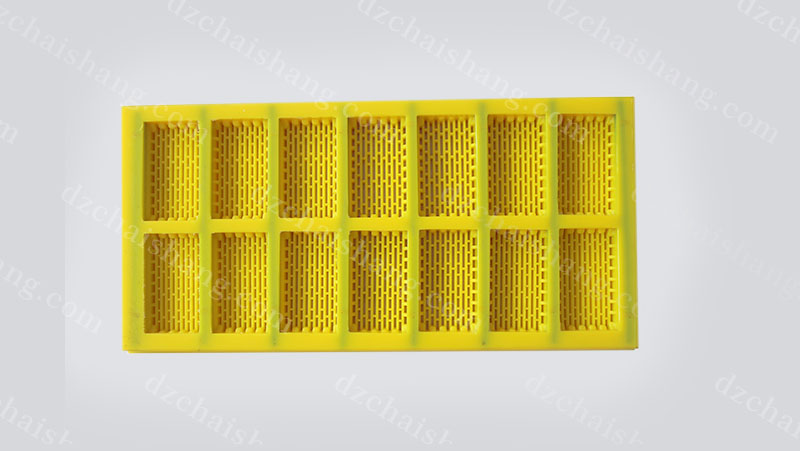
polyurethane is one of the most popular materials used for tailings dewatering screen meshes. Known for its exceptional durability and flexibility, polyurethane can withstand harsh abrasive conditions typically found in tailings management. It resists clogging and maintains an excellent open area, ensuring effective dewatering performance. Polyurethane meshes are also highly resistant to wear and tear, which significantly extends their service life compared to other materials. However, the initial cost of polyurethane screen meshes can be relatively high, which might be a consideration for operations with stringent budget constraints. Stainless steel is another viable option for tailings dewatering screen meshes. It offers superb strength and excellent resistance to rust and corrosion, making it suitable for both wet and dry applications. Stainless steel meshes provide high tensile strength, which is crucial for handling the heavy loads associated with tailings processing. Additionally, they maintain their structural integrity under high temperatures and chemical exposures. While stainless steel meshes are generally more affordable than polyurethane, they are susceptible to blinding and may require more frequent cleaning or replacement, potentially increasing the operational costs over time. rubber screen meshes are also used in tailings dewatering applications, particularly where noise reduction is a priority. Rubber is less noisy than metal screens and offers good wear resistance and flexibility. It effectively absorbs impact, which helps in reducing the breakdown of materials during the screening process, thus preserving the integrity of both the screen and the material being processed. rubber screens are generally cheaper than polyurethane and can be a cost-effective solution for operations where durability is not the primary concern. When comparing these materials, it is essential to consider not only the direct costs associated with purchasing and installing the screen meshes but also the long-term operational costs. For instance, while polyurethane and stainless steel might have higher upfront costs than rubber, their durability and efficiency can lead to lower overall costs in terms of maintenance, replacement, and downtime. Moreover, the choice of material should also be influenced by the specific requirements of the tailings dewatering process. Factors such as particle size, abrasiveness of the material, chemical exposure, and environmental conditions should all be taken into account. For example, in environments where chemical exposure is a concern, stainless steel would be preferable due to its superior corrosion resistance. On the other hand, in applications where wear life and noise are critical factors, polyurethane or rubber might be more suitable. In conclusion, selecting the right material for tailings dewatering screen meshes involves a balance between performance and cost. Each material offers distinct advantages and limitations, and the optimal choice depends on a comprehensive analysis of both the operational conditions and economic factors. By carefully evaluating these aspects, mining operations can enhance their dewatering efficiency, optimize costs, and contribute to more sustainable practices in tailings management.