Advantages Of High-Quality Mine PU polyurethane Subdivision screens In Mineral Processing
High-quality mine PU polyurethane subdivision screens, commonly referred to as PU polyurethane screens, are increasingly becoming integral components in the field of mineral processing. These screens, known for their durability and efficiency, offer numerous advantages over traditional screening materials like wire mesh and steel.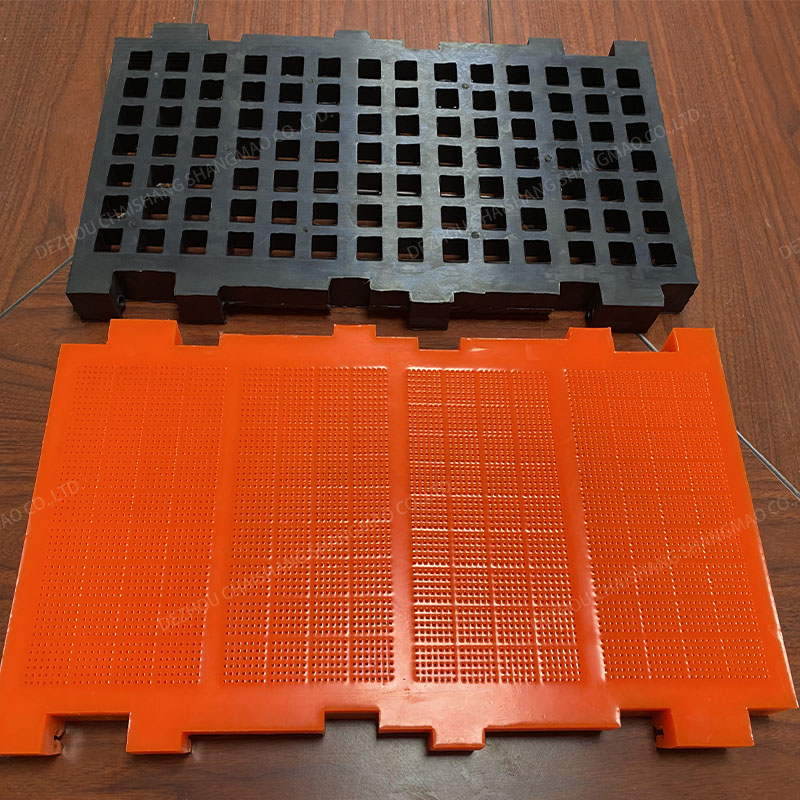
Comparison Between PU Polyurethane Screens And Traditional Screening Materials For Mining Applications
High-quality mine PU polyurethane subdivision screens, commonly referred to as PU polyurethane screens, are increasingly becoming the preferred choice for mining applications, offering significant advantages over traditional screening materials such as steel wire mesh, rubber, and other synthetics. This comparison aims to elucidate the benefits and potential drawbacks of PU polyurethane screens in contrast to these conventional materials, providing a comprehensive understanding of why the shift towards polyurethane technology is not just a trend, but a substantial improvement in mining screen technology. PU polyurethane screens are renowned for their exceptional durability and resistance to wear and tear. Unlike traditional steel wire mesh, which can suffer from rapid degradation due to corrosion and abrasion, polyurethane is inherently resistant to both, thereby extending the lifespan of the screens significantly. This durability not only reduces the frequency of screen replacements but also minimizes downtime, enhancing overall productivity in mining operations. Furthermore, the resilience of polyurethane to various environmental factors such as temperature fluctuations and moisture further solidifies its superiority in durability compared to materials like rubber, which can degrade under extreme conditions.Transitioning from durability to efficiency, PU polyurethane screens exhibit superior performance in screening applications. The flexibility of polyurethane allows for a more effective vibration of the screen, which enhances the screening process by reducing blinding and pegging typically encountered with rigid screening materials like wire mesh. This flexibility ensures that the screen can handle varying feed materials with greater efficiency, thereby improving the quality of the screened output. Additionally, the smooth surface of polyurethane screens minimizes the adhesion of particles to the screen, further facilitating a cleaner and more consistent product. Moreover, the noise reduction capabilities of PU polyurethane screens present a notable advantage over traditional materials. Mining environments are often loud, and the reduction of noise contributes significantly to a more bearable and safer workplace. Polyurethane absorbs sound much better than metal or rubber, which can contribute to a decrease in noise pollution around screening operations. This not only improves the working conditions but also helps in complying with increasingly stringent environmental regulations regarding noise control. However, while the benefits of PU polyurethane screens are compelling, it is also important to consider any potential limitations. One of the primary concerns is the initial cost investment. Polyurethane screens are generally more expensive upfront than traditional wire mesh or rubber screens. This higher initial cost can be a deterrent for some operations, especially those with limited budgets. Nevertheless, it is crucial to consider the long-term savings provided by polyurethane’s extended lifespan and reduced maintenance needs, which often justify the initial expenditure. In conclusion, when comparing PU polyurethane screens with traditional screening materials for mining applications, it becomes clear that polyurethane offers a host of advantages, including enhanced durability, improved screening efficiency, and reduced noise levels. While the cost factor may seem like a drawback, the long-term benefits and operational efficiencies gained from using high-quality mine PU polyurethane subdivision screens make them a wise investment for modern mining operations seeking to optimize their screening processes and overall productivity. As the mining industry continues to evolve, adopting advanced materials like polyurethane is pivotal in meeting both the operational demands and environmental responsibilities of the future.